Case Study: Applying Technology to Warehouse & Logistics Management Systems
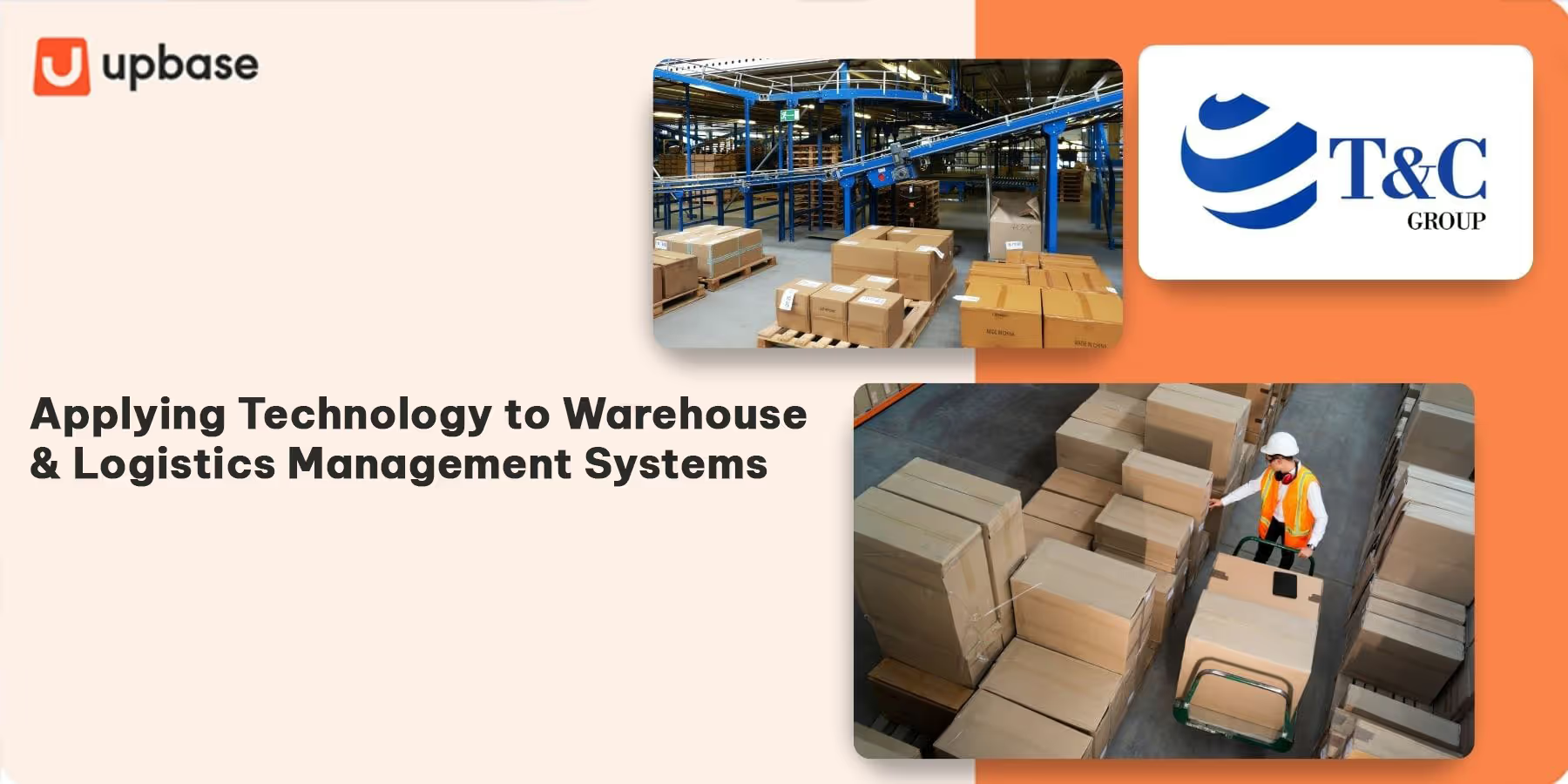
In the logistics industry—especially in warehouse and fulfillment management—accuracy and order processing speed play a critical role in operational efficiency and customer satisfaction. As warehouse operations scale up, relying on manual methods or non-specialized tools becomes a major barrier, leading to inventory losses, delayed order processing, and increased operational costs.
T&C Logistics—a leading provider of warehousing and transportation services in Vietnam—faced similar challenges while operating a 25,000m² warehouse system in Ho Chi Minh City. In response to the need for process optimization, improved efficiency, and reduced errors, T&C decided to implement the professional warehouse management software UpS. This solution not only helped the company digitize its entire operational workflow but also laid the foundation for sustainable business expansion.
This case study will provide a detailed analysis of how T&C Logistics applied the UpS software in warehouse management, the key challenges they needed to solve, and the tangible results achieved through technology adoption.
Introduction to T&C Logistics and Industry Context
T&C Logistics is a leading company in the warehousing and transportation sector in Vietnam, serving thousands of eCommerce businesses. As the Southeast Asian logistics market is projected to reach USD 55 billion by 2025 (Statista), T&C faces the pressing challenge of optimizing operations, minimizing errors, and improving efficiency to maintain its competitive edge.
Overview of T&C Logistics
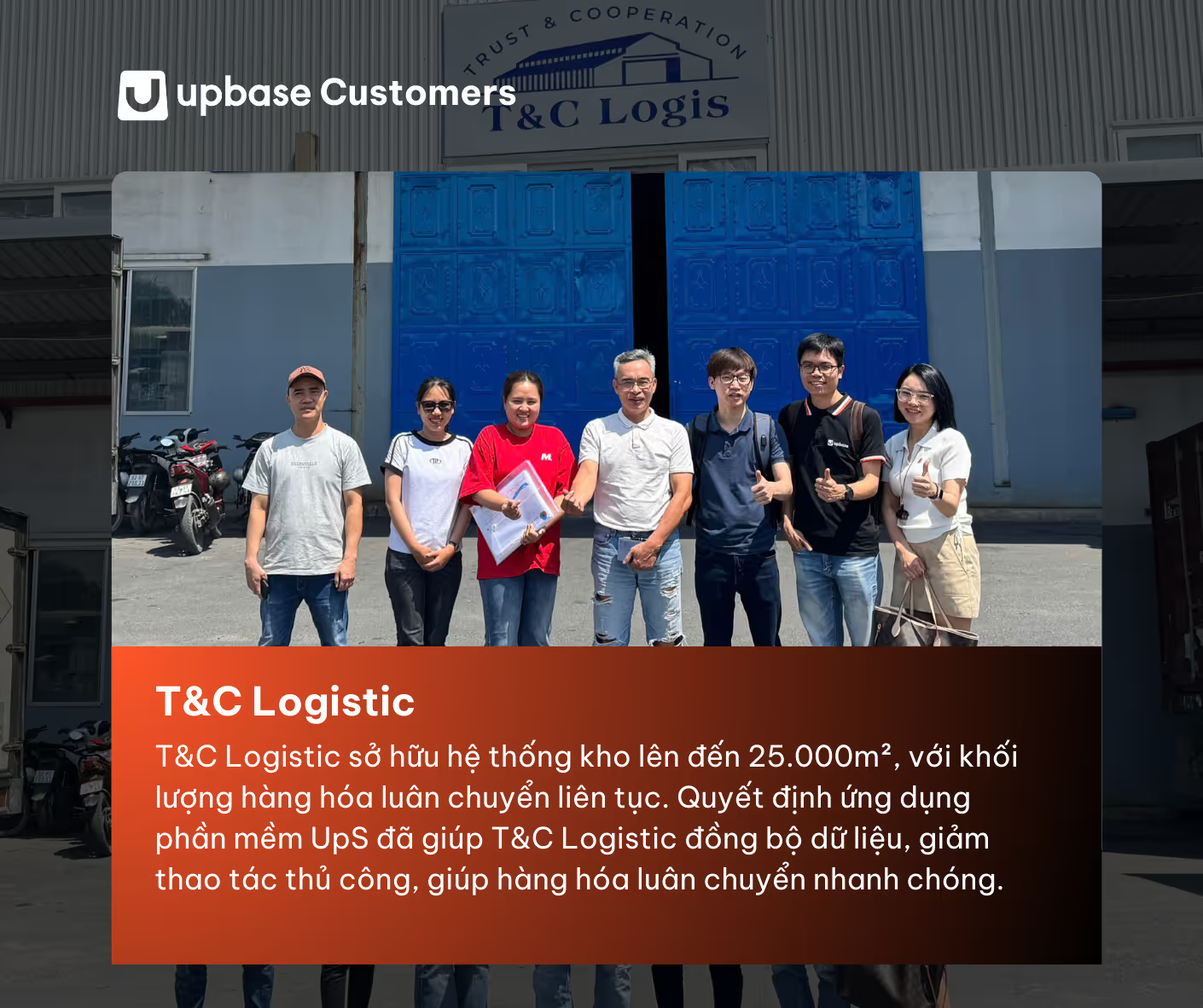
T&C Logistics is one of the leading companies in the warehousing and delivery sector in Vietnam, specializing in comprehensive logistics solutions—from goods storage and order processing to transportation and delivery. With a 25,000m² warehouse system in Ho Chi Minh City, T&C serves a wide range of clients, including eCommerce businesses, retailers, distributors, and manufacturers.
As a strategic partner to many major brands, T&C Logistics is committed to providing modern warehouse operations, cost-optimized solutions, and ensuring high accuracy in every order. However, with rapid business growth, the company has faced numerous challenges in warehouse management and fulfillment operations.
Logistics and Warehouse Management Industry Landscape
The logistics industry is experiencing strong growth driven by the boom in eCommerce and increasing demand for fast delivery. According to Statista, the logistics market in Southeast Asia is projected to reach USD 55 billion by 2025, with Vietnam emerging as one of the most promising markets in the region.
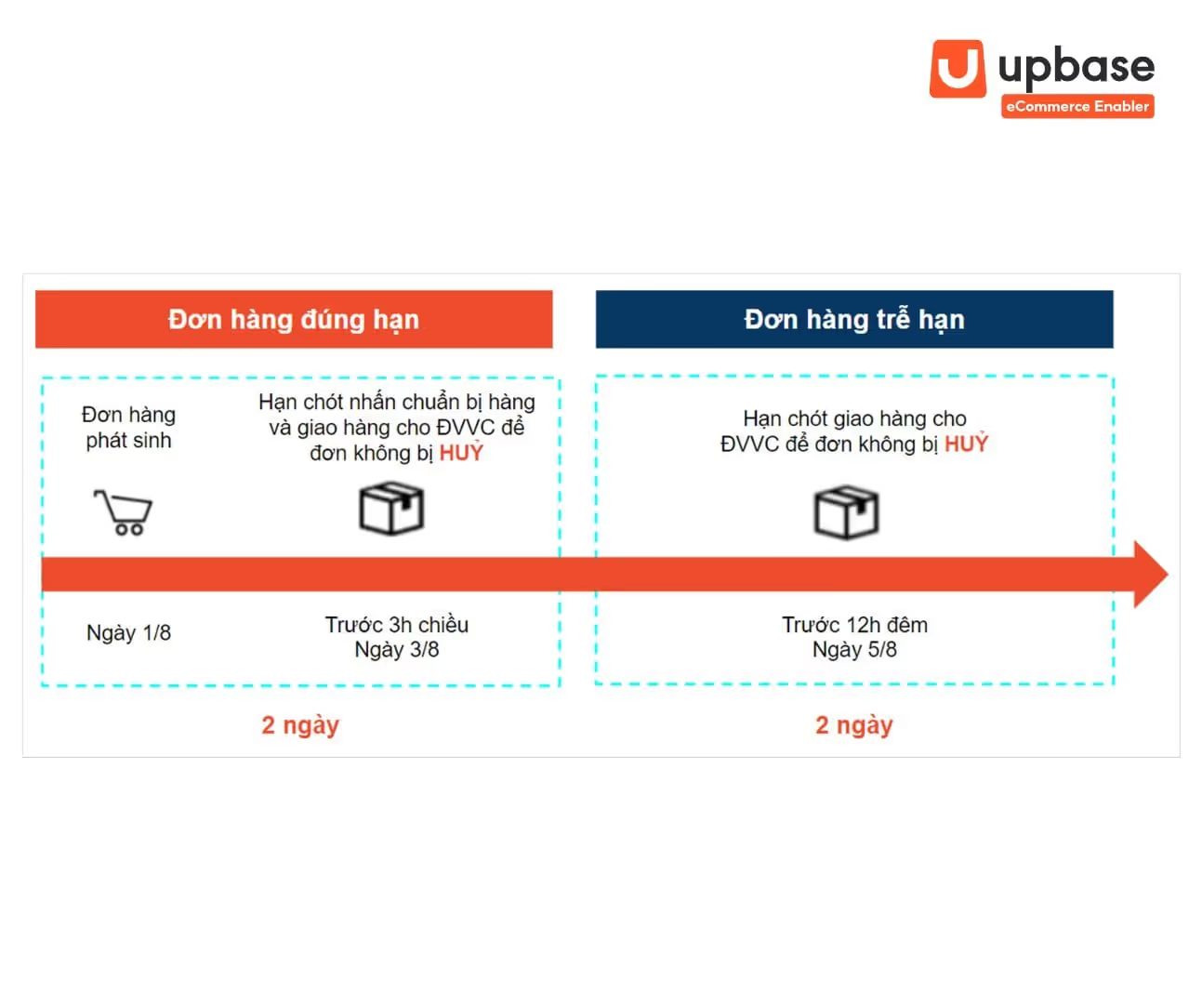
The industry’s growth has brought increasingly high demands for warehousing services:
- Faster order processing is required to meet same-day or 24–48 hour delivery expectations (as per eCommerce platform SLAs).
- Accurate inventory management is essential to avoid stockouts or excess inventory, both of which can negatively impact cash flow.
- Operational cost optimization is critical, especially as labor and facility costs continue to rise.
- Technology integration is needed to boost efficiency, ensure transparency, and minimize errors in inbound and outbound processes.
In this context, applying technology in warehouse management is no longer optional—it has become a necessity for logistics companies to maintain their competitive edge. This was the driving force behind T&C Logistics’ decision to implement UpS—a specialized warehouse and fulfillment management software for eCommerce—designed to optimize operations and enhance productivity.
The Challenge T&C Faced Before Implementing UpS
As a large-scale warehousing and fulfillment provider, T&C Logistics handles 15,000–30,000 orders per day for various eCommerce businesses. However, before deploying the UpS warehouse management software, their operations faced multiple issues, particularly in shipping label printing and order processing.
Slow shipping label printing
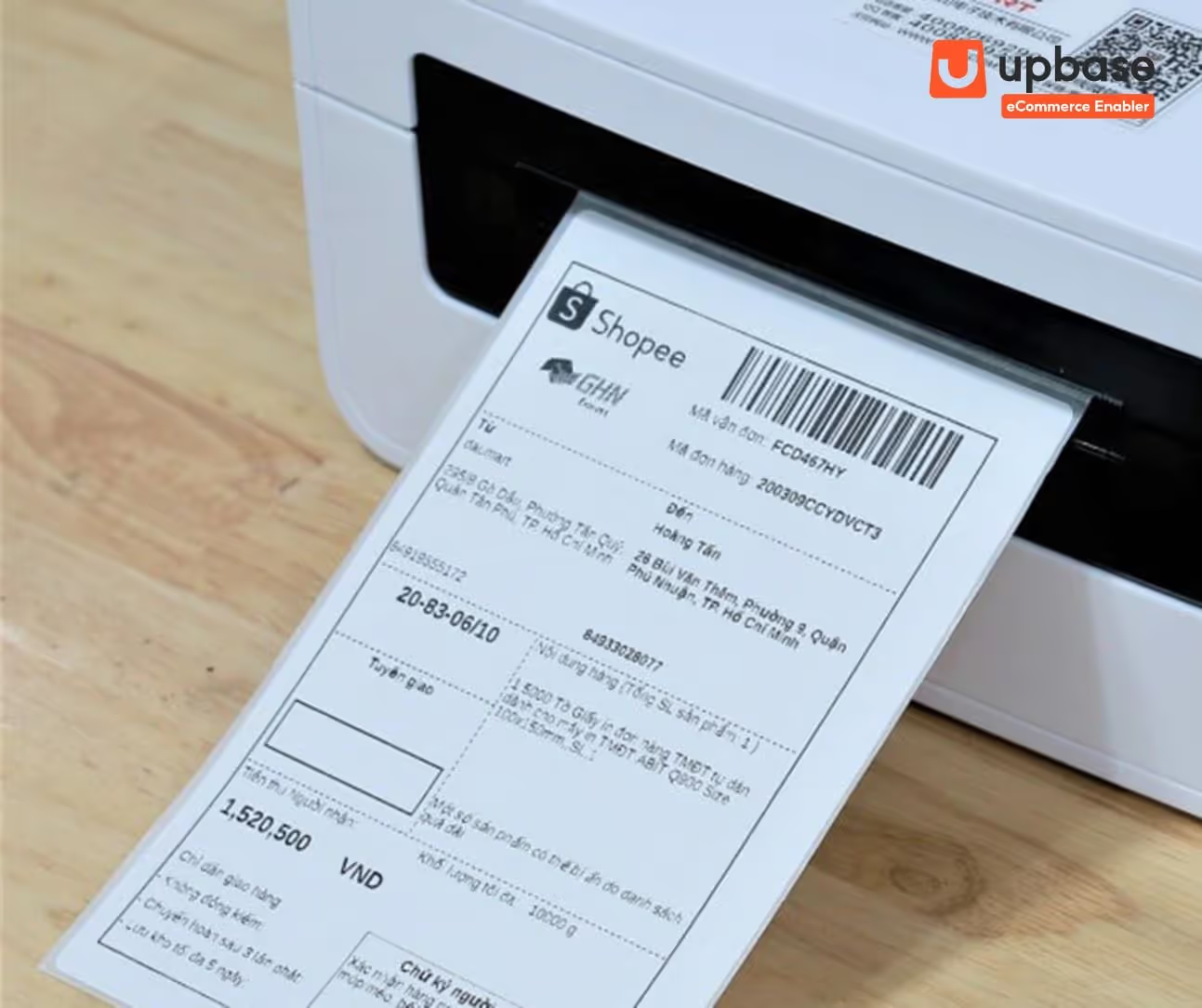
With a high volume of daily orders, T&C’s warehouse needed to print shipping labels in bulk to accelerate the packing process. However, the old system in use only allowed a maximum of 100 labels per batch, leading to several issues:
- When needing to print 500–1000 labels, staff had to split the job into 5–10 separate print runs.
- Time-consuming manual operations: Staff had to wait for one batch to finish before starting the next, slowing down the overall workflow.
- High risk of interruptions: System overloads could cause errors or sudden stoppages, forcing staff to restart the entire printing process.
Slow label printing led to warehouse staff idling while waiting, which disrupted the packing and handover process. Additionally, if orders were not handed over to shipping partners on time, T&C risked violating SLA commitments—potentially harming their service reliability.
Manual Processing of Orders with Free Gifts
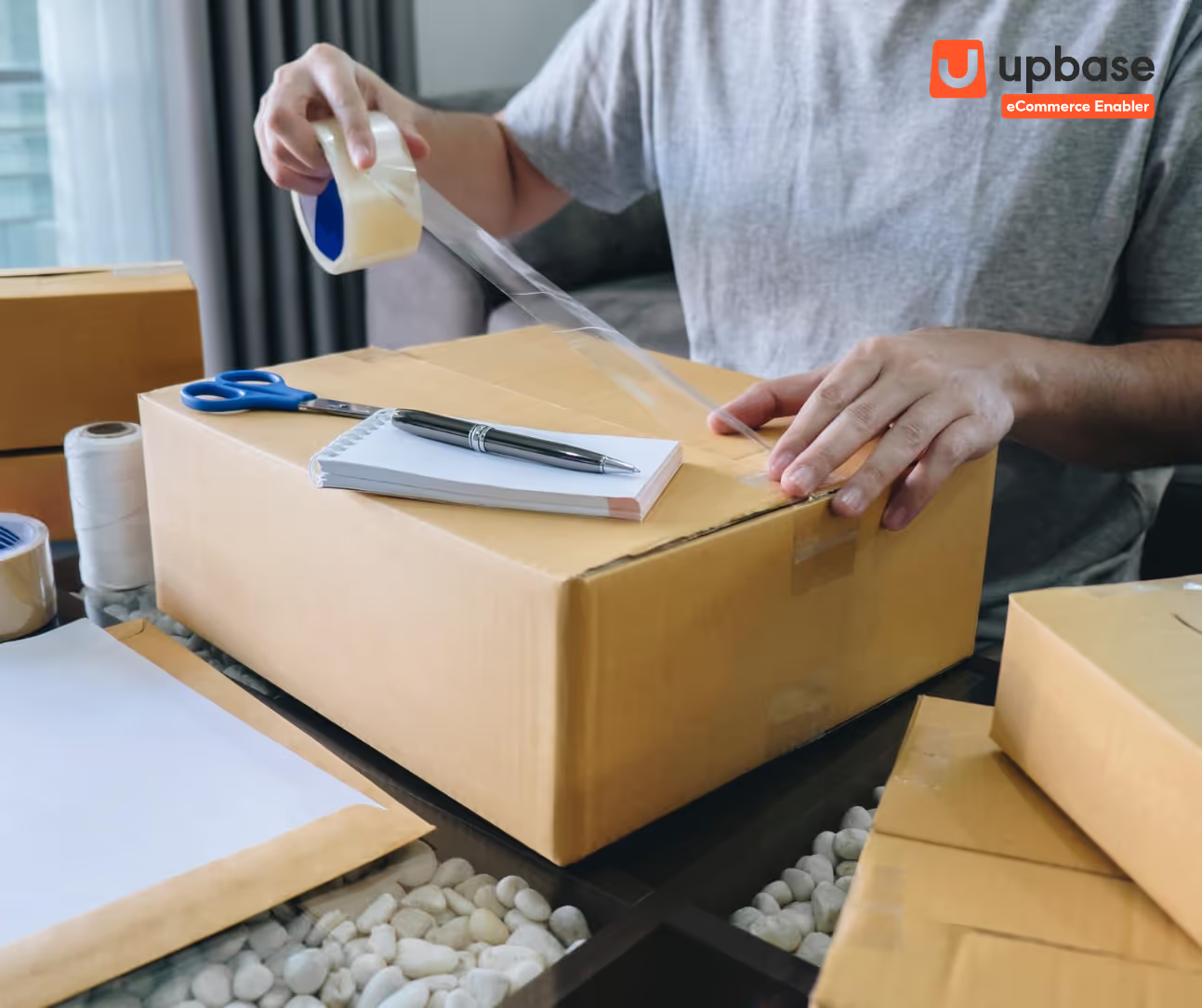
T&C Logistics serves a wide range of eCommerce businesses, many of which include gift items bundled with purchased products. However, their previous system lacked proper support for managing gift items, leading to several operational challenges:
- Gift information not displayed on shipping labels: Warehouse staff had to print a separate gift list and manually cross-check each order, which was time-consuming and prone to errors.
- Manual and complex gift packing process: Since the system didn’t automatically recognize gifts per order, staff had to check manually, which extended the packing time and increased the risk of missing or incorrect gift inclusion.
- No accurate verification process: The absence of a confirmation step for gift inclusion before packing led to a higher rate of customer complaints, negatively impacting the shopping experience and the reputation of businesses using T&C’s services.
Real-life example: When a cosmetics brand launched a campaign offering free samples with every order, T&C’s warehouse staff had to manually check a separate gift list and add the samples by hand. If mistakes occurred, customers might receive the wrong or missing gifts, leading to higher return rates and complaints.
Incorrect Product Packing – Missing Product Verification Before Packing
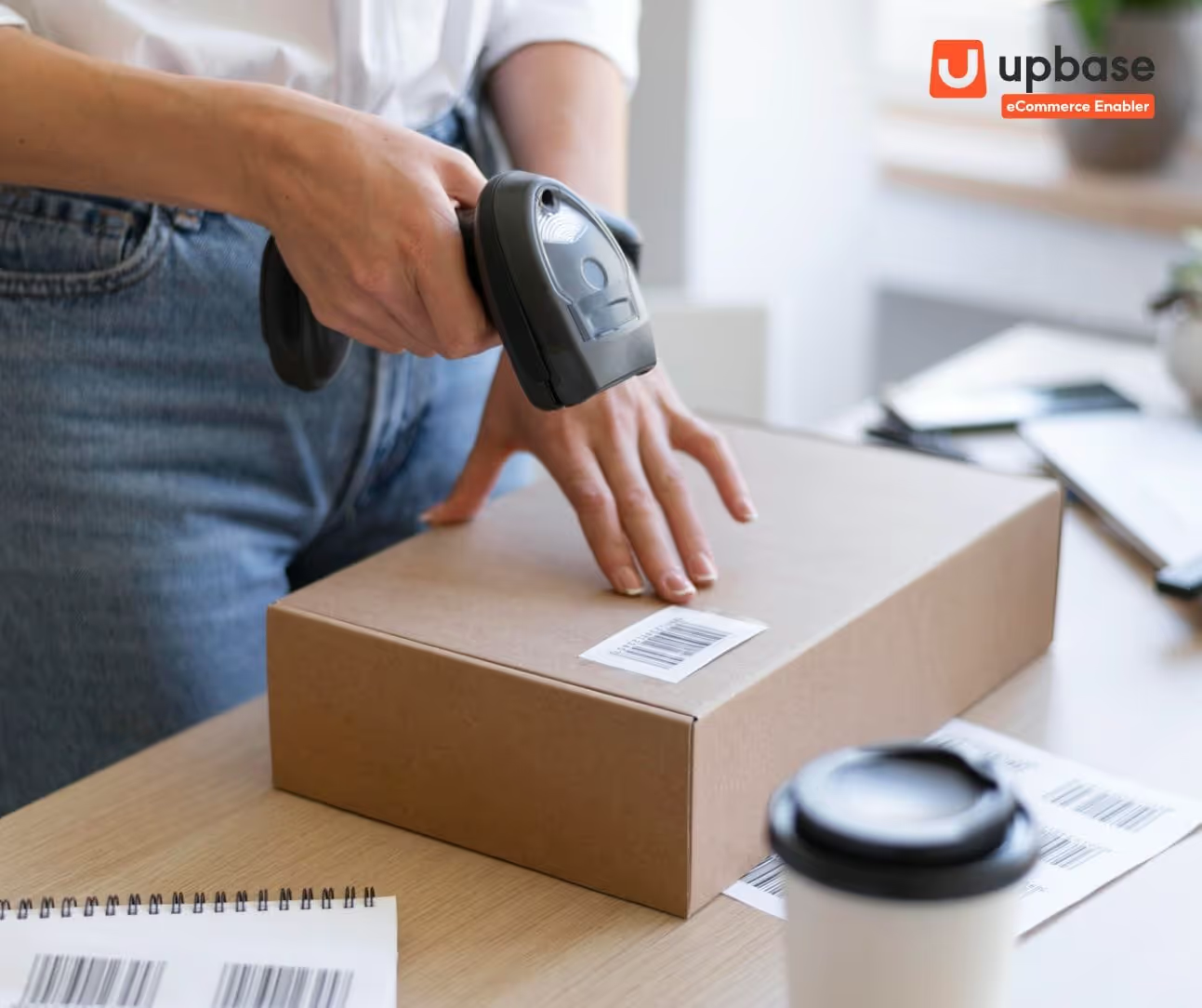
One of the biggest challenges T&C faced before implementing UpS was a high rate of product mix-ups during packing. The main reason was the lack of an automated verification mechanism in the old system, leading to frequent errors in the fulfillment process.
Specific issues included:
- No barcode scanning step to verify products before packing: Warehouse staff had to rely on printed order lists or computer screens to check items, which often led to mistakes—especially with similar products that only differ by variants like color or size.
- Manual checks slowed down order processing speed: As order volume increased, staff had to spend significant time manually verifying each product. For multi-item orders, this process took even longer, impacting delivery timelines.
- No alerts for incorrect product packing: Since the old system didn’t match items against the order automatically, mistakes were only discovered after customer complaints. This resulted in increased return/exchange costs, disrupted operations, and damaged T&C’s reputation.
Manual Inventory Reports – No Real-Time Data
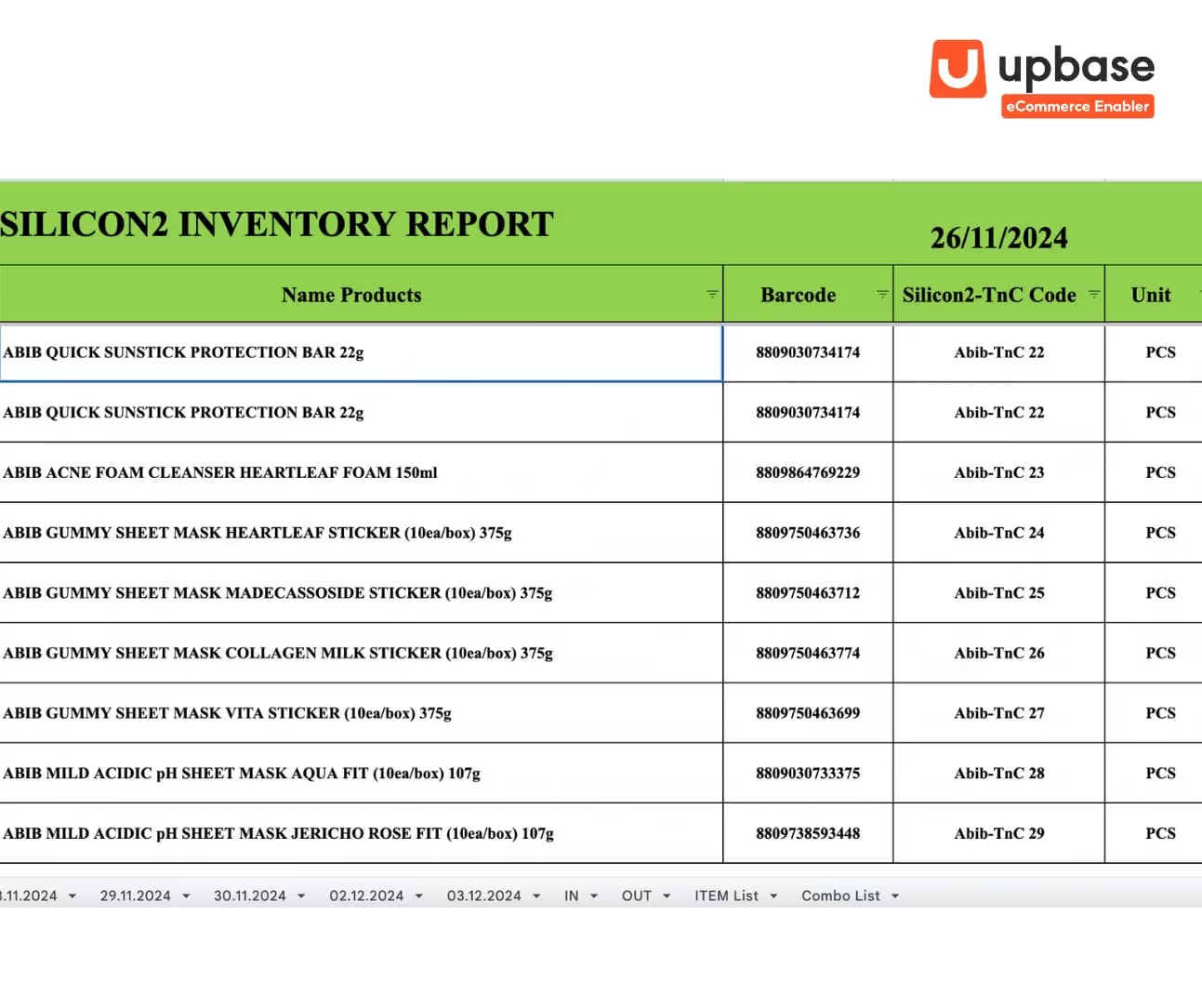
Before using UpS, T&C Logistics managed and reported inventory manually using Excel files, which led to frequent errors and data discrepancies, making it difficult to accurately track the actual stock levels in the warehouse.
- Slow and unsynchronized inventory updates: Stock data was entered manually at the end of the day, failing to reflect real-time inventory levels. This made it difficult for warehouse staff to allocate and manage stock efficiently.
- No alerts for low or aging inventory: Without automated notifications, stockouts or prolonged inventory storage were common, leading to missed sales opportunities or wasted resources.
- Difficult inventory control during peak seasons: During sales seasons, order volumes surged, but due to delayed data updates, discrepancies occurred and slowed down order processing.
Solution: Implementing the UpS Warehouse & Logistics Management Software
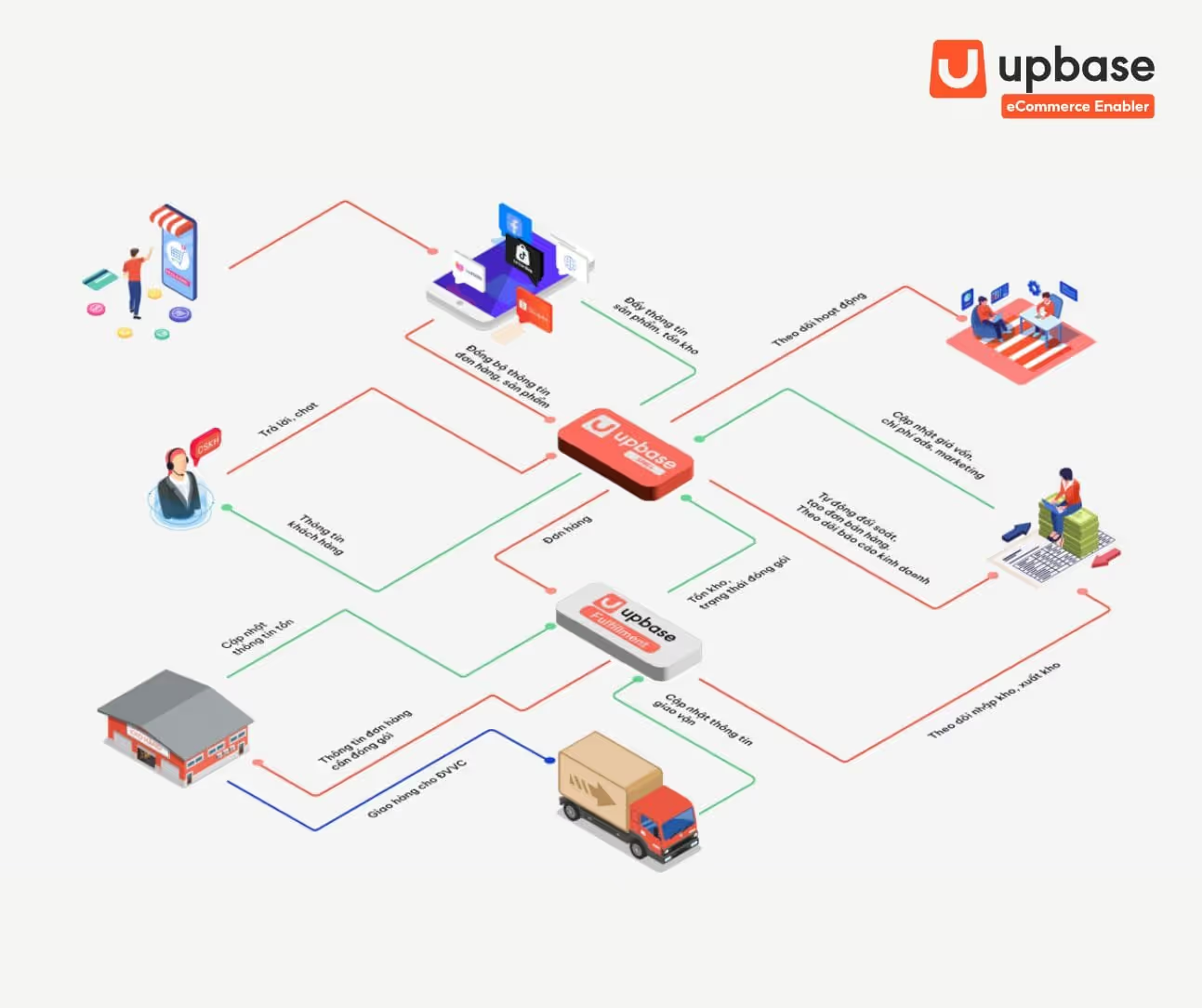
After analyzing the challenges in T&C Logistics’ warehouse and fulfillment operations, the UpS team proposed the following solutions to digitize processes and boost operational efficiency:
Solving Slow Shipping Label Printing
T&C’s old system limited label printing to 100 orders per batch, causing delays during peak hours. UpS optimized this process by offering:
- Fast & stable printing: Supports bulk printing of up to 500 orders per batch, helping warehouse staff process orders faster.
- Integrated delivery route information: Automatically groups orders by delivery area, reducing sorting time after printing.
- Direct integration with shipping partners: API connection with carriers ensures accurate label generation per delivery partner.
Auto-Including Gifts on Shipping Labels
The old system did not display gift information on shipping labels, forcing staff to cross-check with separate lists. UpS addressed this by:
- Automatically showing gift items on shipping labels: Ensures staff don’t miss gifts during packing.
- Gift catalog integration: Each order displays the gift list alongside the main items, reducing packing errors.
- Optimized packing workflow: Eliminates manual steps, speeding up order handling.
Reducing Packing Errors
Previously, the lack of a product verification step led to frequent packing mistakes. UpS improved this with:
- Integrated barcode scanning: Each product is scanned before being boxed, ensuring accuracy.
- Error alerts for mismatched items: The system automatically detects and flags any discrepancies.
- Automated verification process: Eliminates manual checking errors, enhancing precision.
- Real-Time Inventory Reporting
Manual inventory reporting caused delays and inaccuracies. UpS resolved this with:
Real-time inventory sync: Stock levels are updated automatically with every inbound/outbound movement.
Low stock alerts: Notifies managers when inventory reaches minimum levels, ensuring timely replenishment.
Automated reporting: Visual, data-rich dashboards support quick and informed decision-making.
Results After Implementing UpS in Warehouse & Logistics Management
Following the implementation of the UpS warehouse and logistics management software, T&C Logistics achieved significant operational improvements:
- Tripled order processing and label printing speed, with 100% of gift orders handled automatically—eliminating the need for manual cross-checking.
- Reduced packing time by 40% thanks to direct gift data integration into the system.
- Minimized packing errors related to missing or incorrect gifts, improving customer satisfaction.
- Packing error rate dropped by 90% with the barcode scanning verification step, significantly reducing return and exchange costs.
- 24/7 real-time inventory sync eliminated data discrepancies caused by manual entry.
- Inventory audit time reduced by 70%, optimizing staffing and operational costs.
- Timely low-stock alerts ensured products were always available to meet customer demand.
With UpS, T&C Logistics not only resolved long-standing operational issues but also enhanced overall performance—positioning the company for scalable growth as demand continues to rise.
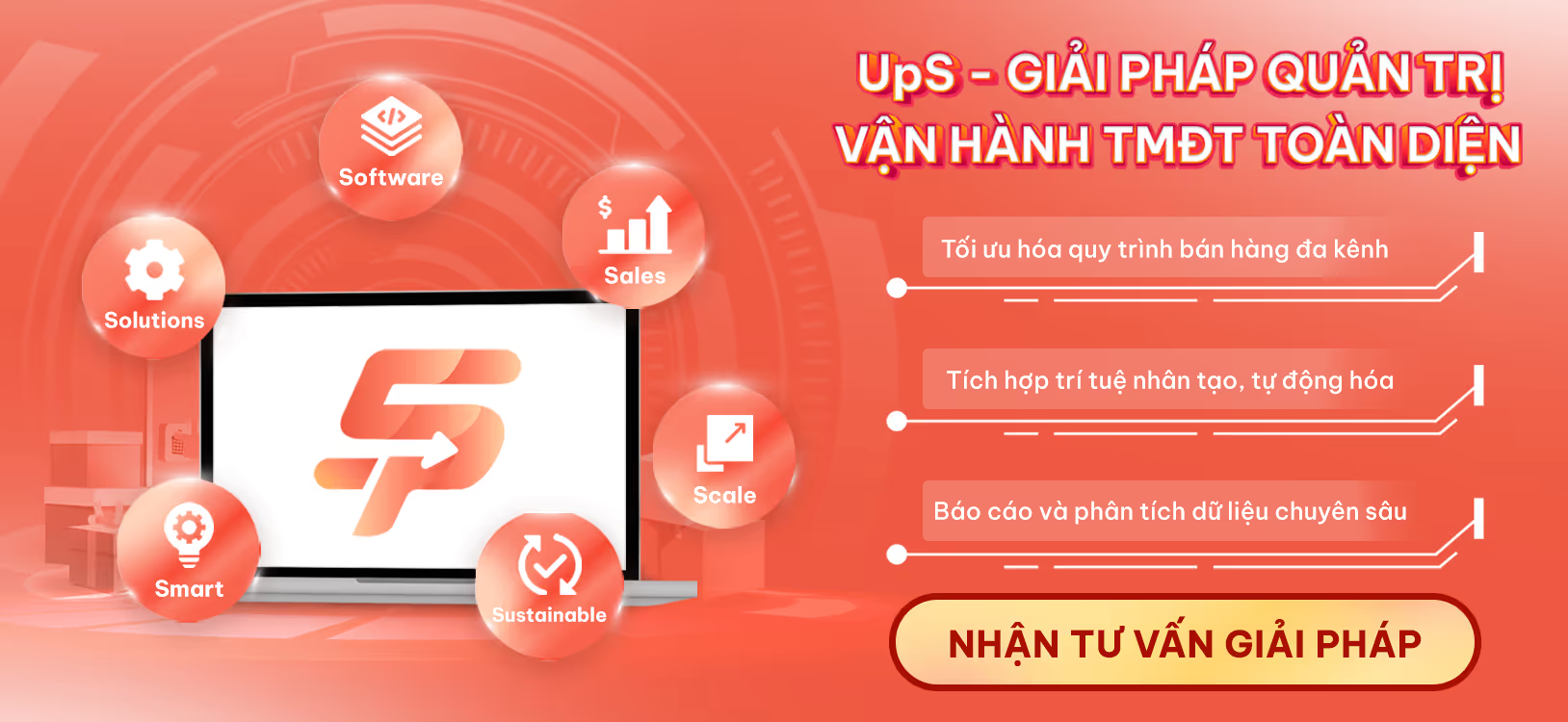
T&C Logistics and many other companies have successfully embraced technology for warehouse and logistics management—what about your business?