Warehouse operations are a key factor in the success of retail businesses in general and e-commerce operations in particular. Many businesses encounter issues in warehouse management that affect business performance, costs, and customer experience. Below are some common mistakes and effective solutions that UpBase would like to share with businesses.
Why do businesses need warehouse operations management?
Warehouse operations management is a core factor in ensuring effective and sustainable business operations, especially for businesses operating on e-commerce platforms. Here are some important reasons why businesses need to focus on warehouse management:
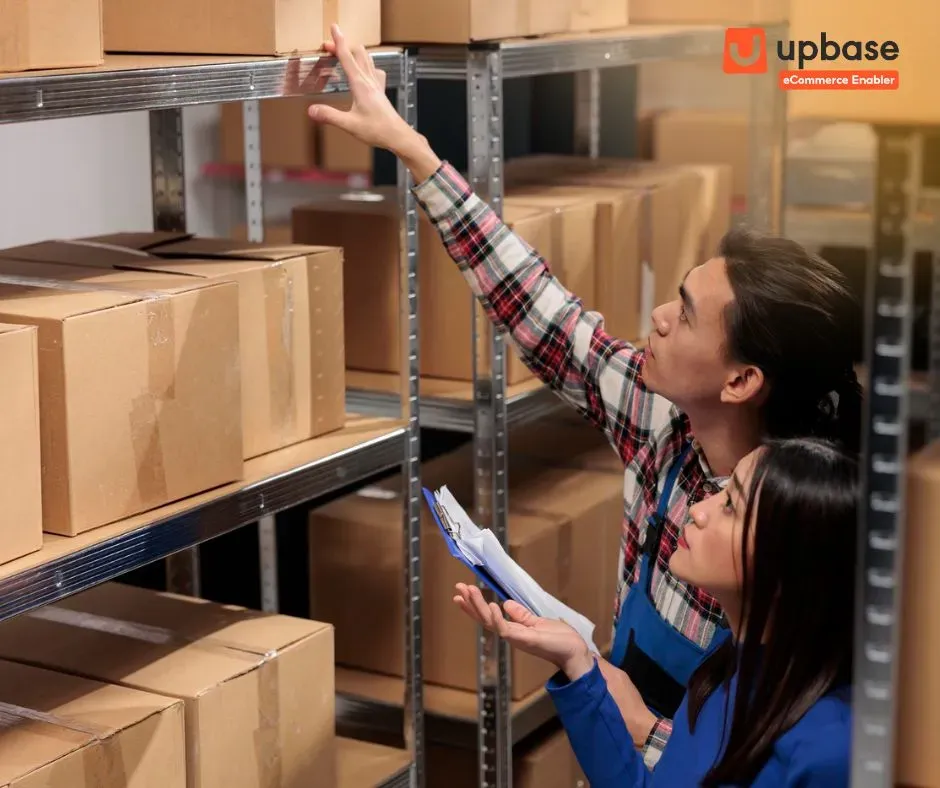
- Ensure Accurate Inventory Management: Warehouse management helps businesses track and control inventory levels accurately, avoiding sudden stockouts or excess product accumulation. This allows businesses to meet customer demand in a timely manner, optimize ordering processes, and manage product stocking efficiently.
- Increase Operational Efficiency: A well-managed warehouse optimizes workflows, reduces time spent searching for and handling products, which in turn enhances employee productivity and overall business efficiency.
- Reduce Operating Costs: By closely managing warehouse operations, businesses can minimize waste, prevent losses due to damaged or expired goods, and reduce storage costs. This helps businesses optimize operational expenses and boost profitability.
- Enhance Customer Experience: Effective warehouse management ensures that products are always available and delivered on time, enhancing the shopping experience for customers. Satisfied customers are likely to return and recommend the business to others, increasing brand loyalty and reputation.
- Ensure Flexibility and Problem-Solving Capability: Efficient warehouse management helps businesses adapt to market fluctuations, such as sudden increases in demand or new trends. This enables businesses to quickly adjust and maintain a competitive edge.
Warehouse operations management is not just about storing and safeguarding goods; it is a crucial strategy for maintaining operational efficiency, reducing costs, and enhancing customer satisfaction. It is a key factor for the long-term success of businesses in the dynamic e-commerce market.
Common Issues Businesses Face in Warehouse Management and Operations
1. Poor Inventory Management
One of the most common issues faced by e-commerce businesses is inaccurate inventory management. Failing to accurately track inventory levels can lead to stockouts or excessive product surplus.
- Inventory Discrepancies: Discrepancies between actual inventory levels and those recorded in the system can result in poor business decisions, delayed shipments, and a damaged reputation, especially during critical times such as promotional campaigns.
- Order Processing Delays: Poor inventory management can lead to incorrect order processing times, causing delays in delivery and negatively impacting the customer experience.
- Inefficient Inventory Rotation: Not rotating inventory properly (FIFO - First In, First Out) can result in products becoming damaged or expired, leading to waste.
2. Inefficient Product Arrangement
Poor layout and arrangement not only reduce warehouse efficiency but also lead to several other issues, such as difficulties in locating products, increased order processing time, and even errors in shipments.
- Difficulty Locating Products: Inefficient arrangement makes it challenging to quickly find products, which can slow down order fulfillment and affect customer satisfaction.
- Underutilized Warehouse Space: Poor layout can lead to suboptimal use of available warehouse space, limiting storage capacity and increasing costs.
- Increased Risk of Product Misplacement: A disorganized warehouse increases the risk of confusion and errors, leading to incorrect shipments and potential customer dissatisfaction.
3 . Errors in Packing and Shipping
Errors in packing and shipping can have serious consequences, such as damaging the company's reputation, increasing return rates, and losing customer trust.
- Incorrect Product Packing: Sending out the wrong product or improperly packed items can lead to customer dissatisfaction and returns.
- Inadequate Packaging: Using unsuitable or insufficient packaging can fail to protect products during transit, resulting in damage and customer complaints.
- Late Deliveries: Failing to meet strict Service Level Agreements (SLAs) and delivering orders late can lead to customer frustration and a negative impact on the business's reliability.
4. Lack of Flexibility in Response
In e-commerce, flexibility is a crucial factor for maintaining stability and growth. However, many businesses struggle with adapting to unexpected situations, such as sudden spikes in order volume, changes in customer demand, or issues arising during warehouse operations.
- Inability to Handle Large Order Volumes Quickly: Especially during sales events or major campaigns, businesses may struggle to manage a surge in orders effectively.
- Slow Response to Changing Customer Demand: Failure to react promptly to shifts in customer needs can lead to missed opportunities and customer dissatisfaction.
- Inadequate Inventory Adjustments: Not adjusting inventory levels in accordance with demand can result in either excess stock or shortages, leading to resource waste and increased operational costs.
5. High Costs
High operational costs pose a significant challenge for businesses on e-commerce platforms, directly impacting profitability and competitiveness. Ineffective management across various areas—such as inventory management, staffing, packaging, and shipping—can lead to increased operational expenses.
- Infrastructure, Location, and Equipment Costs: Investments in warehouse infrastructure, location, and equipment can be substantial.
- Staffing Costs: Expenses related to hiring and maintaining warehouse staff.
- Software Management Costs: Costs associated with using inventory management software.
- Inventory Management Costs: Expenses incurred in managing and maintaining stock levels.
- Maintenance and Operational Costs: Ongoing costs for warehouse maintenance and operations.
6. Building an Operations Team
To ensure smooth and efficient warehouse operations, businesses need to establish a consistent workflow. Develop and document standardized procedures to ensure that all employees understand and carry out their tasks in a uniform manner. The process should include steps from receiving goods, storing, and packaging to shipping.
7. Risk Management and Incident Handling
Develop contingency plans for emergencies or unexpected incidents, such as loss of goods, equipment failures, or staffing crises. Each business should ensure that all employees are aware of the procedures and response measures for warehouse operations.
Effective Warehouse Management Solutions for Businesses
A smoothly operating warehouse system not only helps reduce costs but also enhances customer experience and optimizes overall business performance. To achieve this, businesses need to implement modern and effective warehouse management solutions. UpBase will propose practical solutions to optimize warehouse operations, including improving storage and inventory management processes, optimizing packaging and shipping, and enhancing staff and cost management efficiency.
1. Applying Technology to Warehouse Management
Effective warehouse management is key to maintaining smooth operations and swiftly responding to customer demands. The UpBase SMEs multichannel sales management software is an advanced solution that helps businesses optimize their warehouse operations comprehensively.
UpBase SMEs offers multichannel integration, allowing businesses to manage their warehouse from various sales platforms synchronously. This helps monitor inventory and orders across online and offline sales channels, minimizing risks and errors related to data synchronization. Here are some useful features of UpBase SMEs that aid businesses in optimizing warehouse management:

- Real-time inventory tracking, providing accurate updates on remaining stock, automatically alerting when inventory levels are low, and supporting effective restocking planning.
- The software automates various warehouse management processes such as receiving, shipping, inventory counting, and reporting.
- It offers powerful data analysis tools to help businesses understand consumer trends and customer demand.
- The software supports order tracking and management, improves packaging and shipping processes, ensuring orders are processed quickly and accurately, enhancing customer satisfaction.
Using UpBase SMEs, businesses can not only enhance inventory management efficiency but also improve competitiveness and respond quickly to market demands. Investing in multichannel sales management software is a crucial step to optimize warehouse operations and achieve sustainable growth in an increasingly competitive business environment.
2. Optimizing Storage and Sorting Processes
The storage and sorting processes within a warehouse play a crucial role in maintaining operational efficiency and optimizing costs. Here are some methods to optimize these processes:
- Classify Inventory: Organize goods based on product categories, consumption frequency, and size. Using appropriate shelving, pallets, and storage areas helps in easy access to items and minimizes clutter in the warehouse.
- Warehouse Management Software: Utilize warehouse management software to track the location of goods, update inventory status, and coordinate sorting processes accurately. Tools such as barcodes, RFID, and WMS (Warehouse Management Systems) enhance accuracy and reduce errors in storage and sorting.
- Apply FIFO or LIFO: Implement methods like FIFO (First In, First Out) or LIFO (Last In, First Out) depending on the type of goods and storage requirements. Ensure that perishable items or those with short shelf lives are handled and sold promptly.
- Establish Clear Procedures and Standards: Develop clear processes and standards for storage and sorting, including guidelines for arranging goods, quality inspection procedures, and inventory checks. Ensure that all employees are trained and adhere to these processes to maintain operational efficiency.
3. Improving Packing and Shipping Processes
The packing and shipping processes are crucial stages in the supply chain, directly impacting customer satisfaction and business efficiency. To optimize these processes, businesses should implement the following improvement measures:
- Ensure Safe and Effective Packing: Use high-quality packing materials suitable for each type of product to protect goods from damage during transportation.
- Apply Lean Methods: Implement lean practices such as 5S (Sort, Set in order, Shine, Standardize, Sustain) and continuous improvement (Kaizen) in the packing process to minimize waste and optimize the procedure.
- Thoroughly Inspect Orders: Ensure that all orders are carefully checked before leaving the warehouse. Utilize warehouse management systems (WMS) to track and verify orders to minimize errors and ensure products match customer orders.
4. Using Fulfillment Services
Using UpBase's fulfillment services will be an optimal solution to enhance your business efficiency. This service not only helps save time and costs but also improves customer service quality. Here’s how UpBase's fulfillment services can improve your warehouse management process:
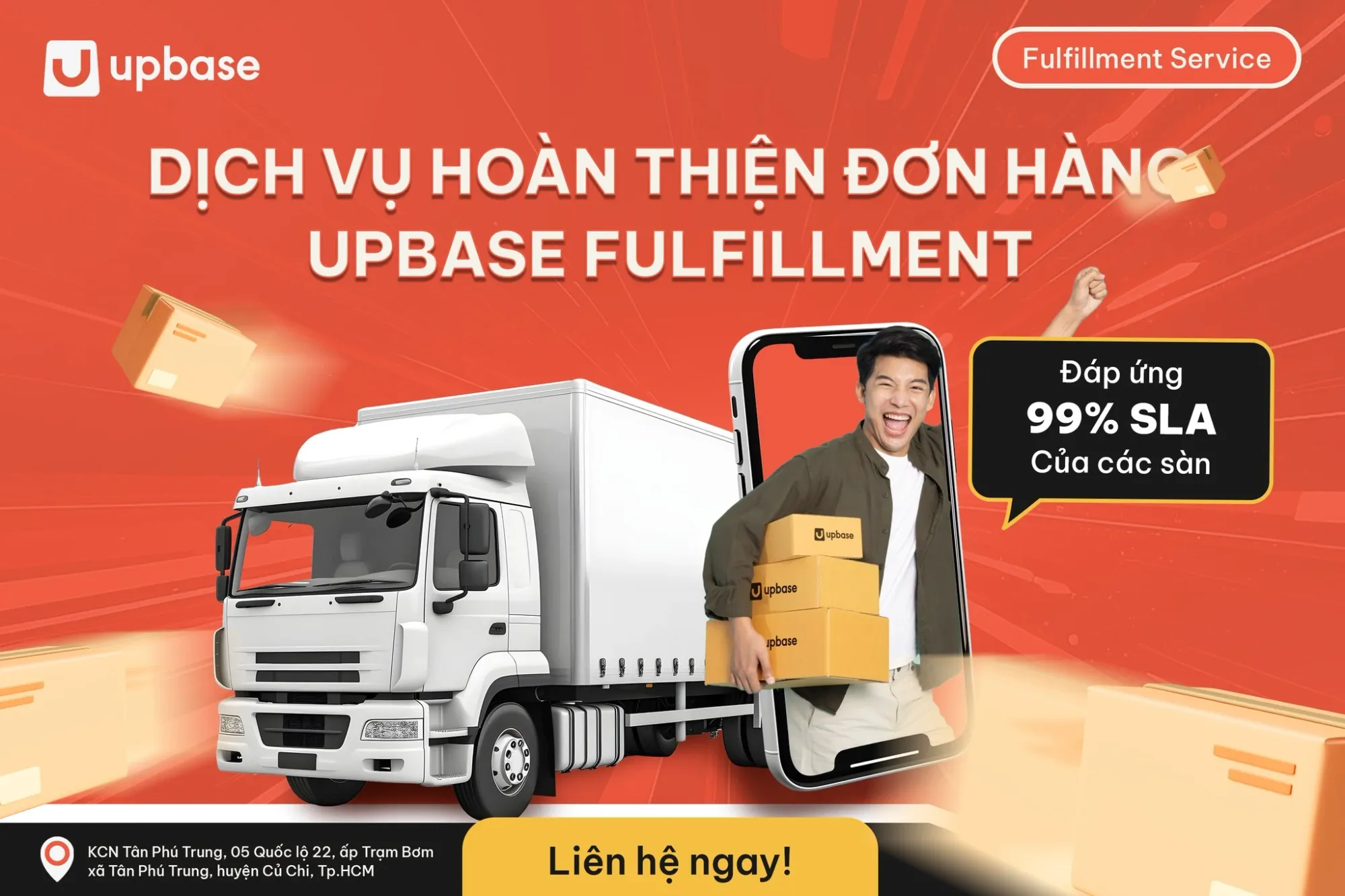
- Optimize Processes: UpBase uses advanced technology and standardized procedures to ensure your goods are processed quickly and accurately. From inventory management to packaging and shipping, this helps businesses save time and costs.
- Reduce Costs: Businesses can cut down on warehouse operating costs, including storage, packaging, and shipping expenses.
- Enhance Customer Experience: UpBase ensures that the packaging, handling, and delivery of orders meet the platform’s SLA standards, providing the best experience for customers.
- Data and Analytics: UpBase provides detailed reports on process performance, helping businesses monitor and optimize their operations.
- Comprehensive Support: UpBase's team of experts is always ready to advise and assist you in optimizing your fulfillment processes, from staff training to technological solutions.
UpBase is not just a fulfillment service provider but a strategic partner that helps businesses enhance operational efficiency and increase customer satisfaction.
Let UpBase be your partner on the path to growth and success. Contact UpBase today to experience our fulfillment services and turn challenges into opportunities!
See more related articles:
What are Self-Fulfillment and Fulfillment Providers? Differences and How They Operate
3 Types of Fulfillment Models & Their Implementation Processes